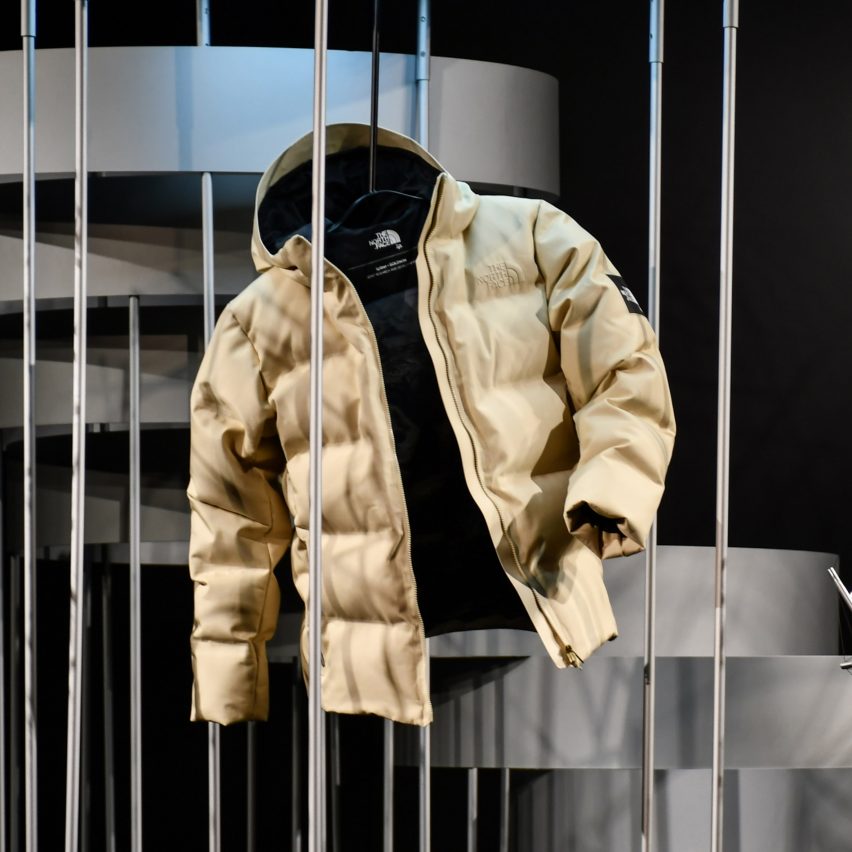
Biotech start-up Spiber and The North Face's Japanese distributor Goldwin have created the first mass-manufactured jacket made from synthetic spider silk.
In total, 50 Moon Parkas have been produced from the emulated spider silk – an artificial material based on the DNA of spider's silk – which keen buyers can enter a lottery to purchase.
Previous garments made using lab-grown spider silk, including the 2015 iteration of the Moon Parka and the Adidas x Stella McCartney Biofabric Tennis Dress, have been created as prototypes, meaning they were not produced at scale and made available for purchase.
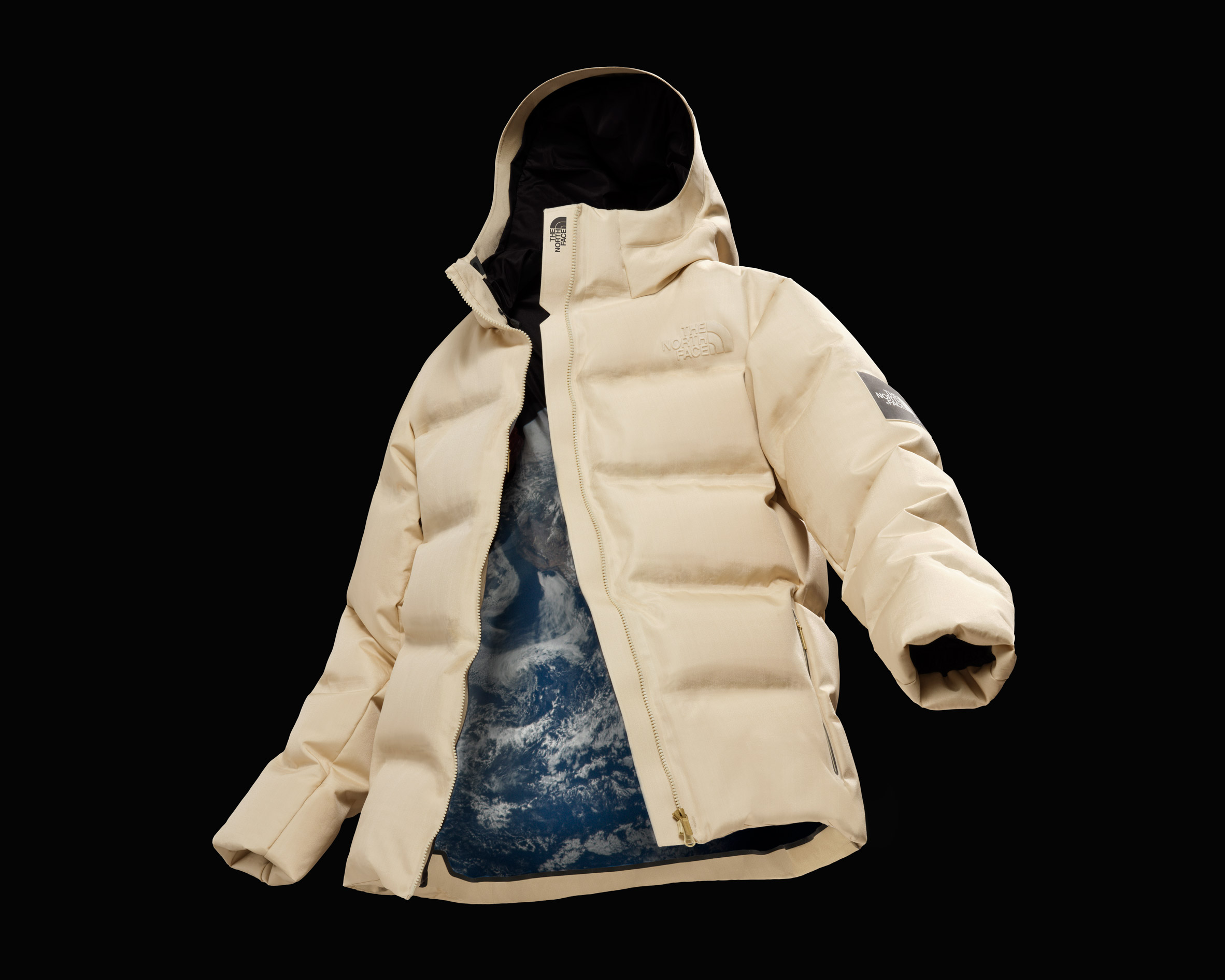
The reason various biomaterial companies have been trying to artificially re-create spider silk, which the animals use to form webs or cocoons, can be attributed to its unrivalled natural properties.
"Spider silk is a protein fiber that has long been somewhat of a holy grail for material scientists because of its unique ability to combine both strength and extensibility in one fiber," said Daniel Meyer, Spiber's head of global corporate planning.
"It has been said that a spider web with threads one centimetre in diameter could stop a jumbo jet in flight," he told Dezeen.
This is an especially appealing prospect for the outer- and performance-wear industry, which traditionally relies on petroleum-based materials such as nylon to create clothing that is durable enough to withstand tough conditions.
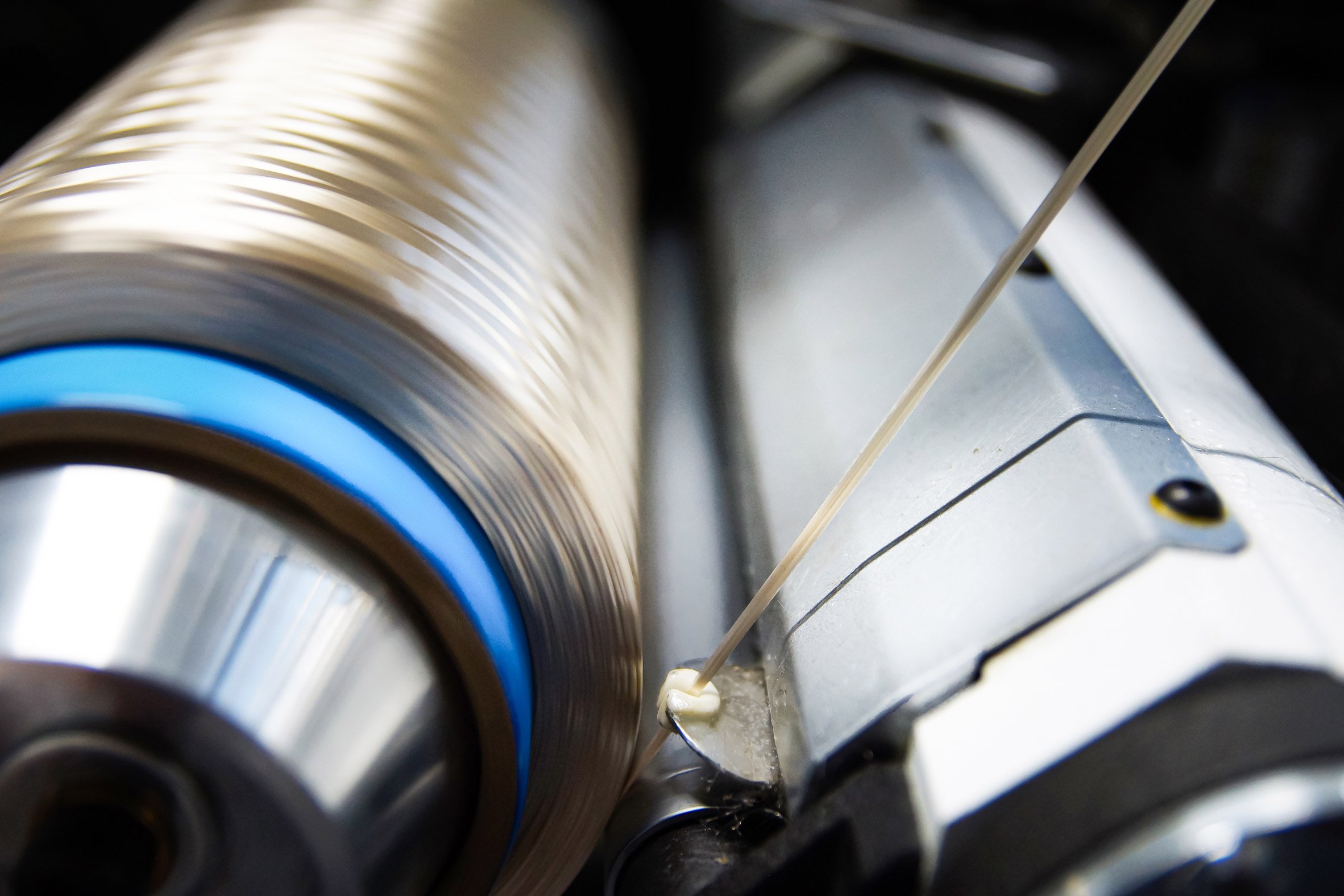
However, due to the cannibalistic nature of spiders, it has been impossible to mass-produce spider silk in the same way as other animal by-products.
Spiber's solution was to re-create the material's molecules from scratch. "We set our eyes upon microbial fermentation as the method to produce spider silk proteins," said Meyer.
"In essence, we would create our own DNA based on the DNA that is responsible for producing spider silk, incorporate that it into microorganisms, and then feed them nutrients in large tanks so that they can multiply and produce the protein of interest."
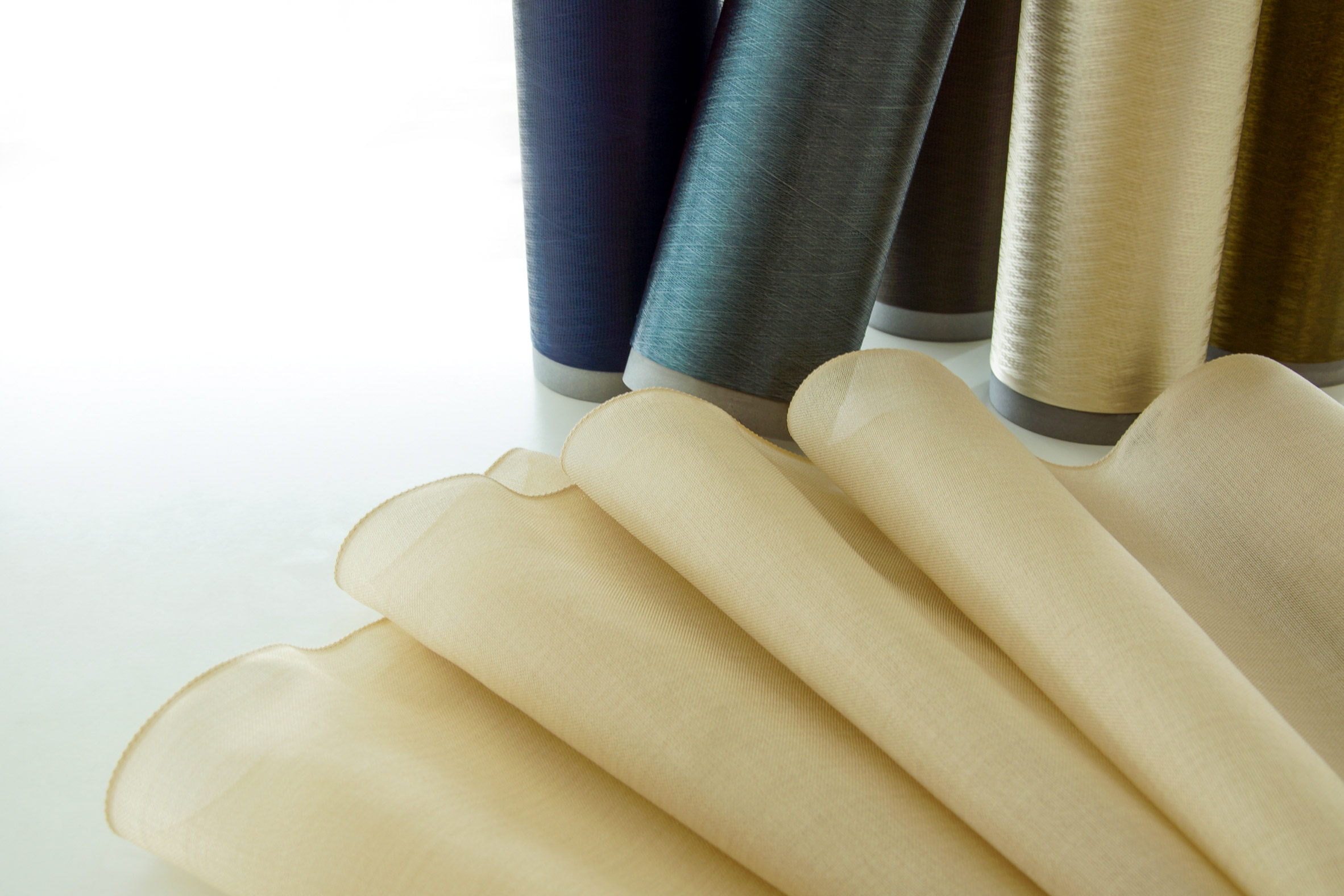
A scaled-up version of this process, using commercial manufacturing equipment to fashion the proteins into yarns, was used for the first Moon Parka prototype. However, for the latest parka an enhanced version of the proteins was created.
"We quickly realised that natural spider silk might be great for some applications, but not so great for others," Meyer recalled.
"For example, it has a property called supercontraction, where water is absorbed and in seconds the silk will shrink by up to 50 per cent. We were aware of this property, but weren’t sure how or if it would carry over to textiles produced in our process. It turns out that it most definitely did."
Over four more years of research, Spiber and Goldwin were able to optimise the protein textile to keep its shape when wet, while making it feasible to manufacture on a mass scale and at a lower price.
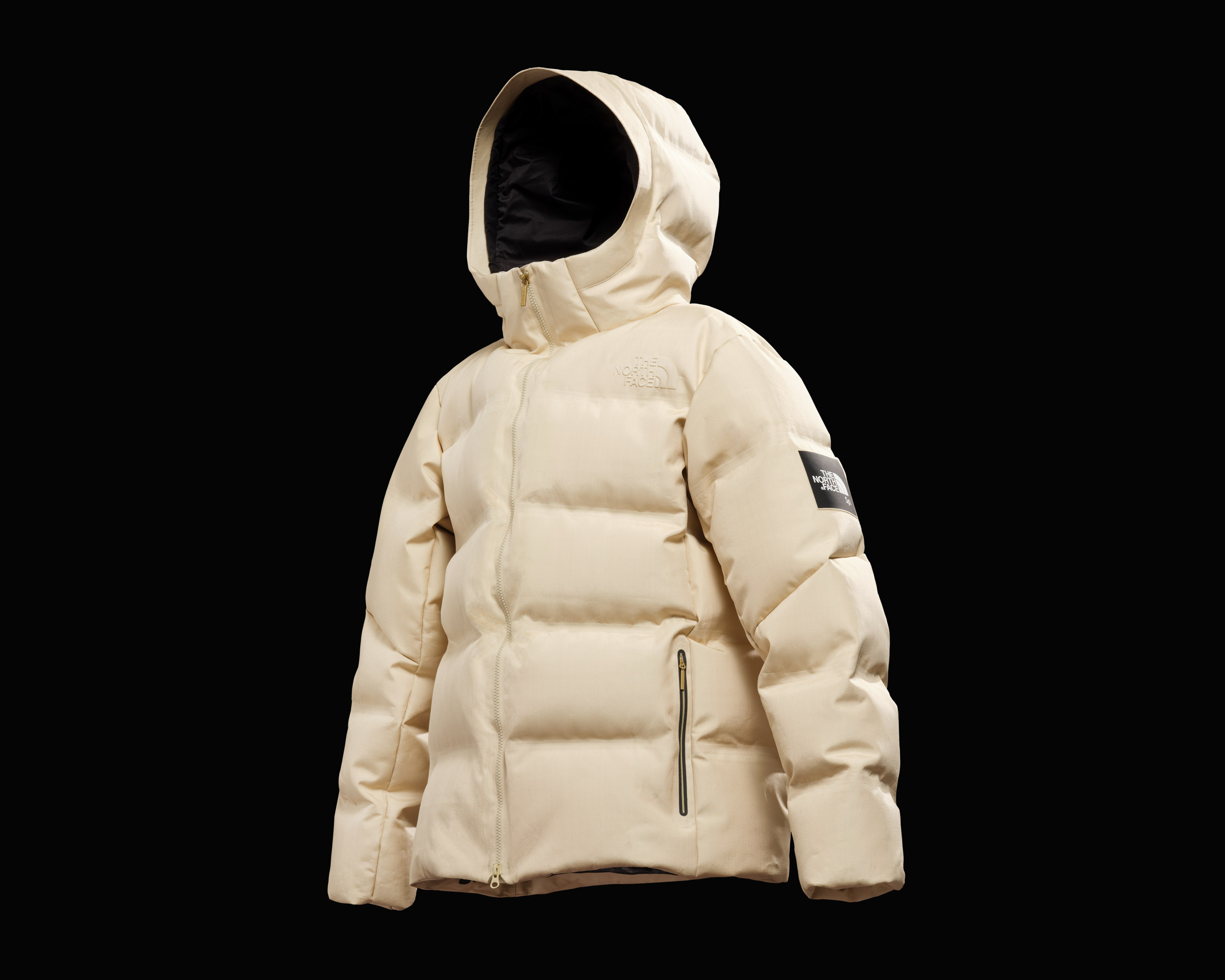
Crucially, this latest version of the parka does not then rely on a one-to-one replication of spider silk proteins. Instead, they are redesigned using gene editing techniques to provide only the desired properties, namely its strength and stretchability.
"We begin by analysing the genetic information responsible for protein production in nature," Meyer explained. "Once we have designed a strand of DNA that we think will provide the properties we want, we incorporate this DNA into a microorganism."
From here, the process remains very similar to that of the initial prototype, wherein the organisms are given sugars and minerals so they can grow and produce the designed protein.

"Once fermentation is completed, we separate our desired protein from the microorganisms, and dry it into a pellet or powder which we call Brewed Protein," Meyer continued.
"This can can then be processed into a variety of materials. In the case of a fibre, the protein powder is dissolved into a solution called a dope, then extruded from a nozzle, after which it is hardened into a fibre."
For the Moon Parka, Spiber spins the proteins into multifilament yarn, which is then woven into a textile by Goldwin and fashioned into the jacket's shell.
This outer layer is the same colour as the webs of golden orb spiders and remains biodegradable, while being waterproof and durable enough to withstand the performance tests, which Goldwin requires all of its petroleum-based jackets to pass.
However a middle layer, made of a breathable laminate, and an inner heat-retention layer which uses the same 900 fill down as The North Face's expedition-use Summit Series, are not biodegradable.
Going forward, the synthetic proteins for the Moon Parka will likely be produced in Spiber's mass production plant in Thailand, which is set to be completed in 2021 with more than £35 million in funding secured.
It will be 100 times larger than Spiber's pilot plant in Japan and is expected to be the world's largest structural protein fermentation facility, capable of producing several hundred tonnes per year.
The post Spiber creates first commercially available jacket from emulated spider silk for The North Face appeared first on Dezeen.
https://ift.tt/31Evuja
twitter.com/3novicesindia
No comments:
Post a Comment